Общая численность компании: 2200 человек.
Как было
Производственный процесс в компании “Биокад” состоит из нескольких этапов: поставка - входной контроль - сертификация - проверка сырья - производство - поставка конечному клиенту. В этой цепочке была затруднена коммуникация между отделами, из-за чего возникало сразу несколько проблем:
- производство в последний момент узнавало о том, что в наличии нет необходимых сертифицированных материалов
- контрольная группа и лаборатории не могли заранее планировать свою загрузку
- “условные” допуски оставались и несли риск для качества готовой продукции, оставалась вероятность, что придется отозвать целую партию препарата после повторной проверки
Это могло приводить к серьёзным убыткам и несло угрозу для репутации компании.
Задача
Компании потребовалось наладить и автоматизировать взаимодействие между отделами для бесперебойного процесса производства. С этой задачей они обратились к нам.
Решение
Мы предложили внедрить систему сертификации на основе уже установленной 1С ERP, с помощью которой весь процесс станет прозрачным и чётко разграниченным по времени проведения каждого этапа. Все сотрудники смогут получить доступ ко всей необходимой информации об этапах производства и при необходимости внести изменения.
Ход работы
Мы начали работу с опроса всех участников процесса производства, начиная от руководителей, директоров и представителей различных служб до простых работников склада и лаборантов для лучшего понимания их взаимодействия. Итогом интервью стала функциональная модель компании, которая описывала все производственные процессы компании и то, как они будут автоматизированы.
Механика
Теперь при обязательной проверке необходимых материалов данные автоматически вносятся в систему, а на упаковку клеится ярлык с указанием, какие пробы были проведены, куда она адресована (лаборатории или производство). В случае нехватки времени на полную проверку, делаются только необходимые пробы, а в системе фиксируется возможность брака в готовом продукте.
Руководители лабораторий и смен на производстве видят какие планируются отгрузки готовой продукции и могут планировать свою работу и нагрузку своих сотрудников, а также запрашивать сырье у закупщиков.
Отдел контроль качества оперативно общается со службой закупок, увеличивая или уменьшая заказ, в зависимости от запросов лабораторий и производства, взаимодействует с производством, изменяя размер будущей партии, исходя из потребностей клиента. При необходимости осуществляются перемещения продукции между складами.
Результат
Так как система стала “прозрачной”, работникам компании стало проще и удобнее в ней работать. Из-за этого стало намного легче следить за качеством продукции, и риск выпуска некачественной продукции на производстве стал крайне низким.
Производство больше не остановится из-за нехватки материалов, потому что всем ответственным за это сотрудникам удобно следить за остатками на складе и вовремя делать следующий заказ. Также это привело к размеренному темпу производства и снижению переработок среди персонала, так как всегда четко видно сколько единиц продукции нужно сделать за смену, чтобы весь заказ был готов к сроку.
А так как качеству и срокам изготовления больше ничего не угрожает, то и риск навредить репутации компании сведен к минимуму!
О сотрудничестве с командой "РАУ АйТи"
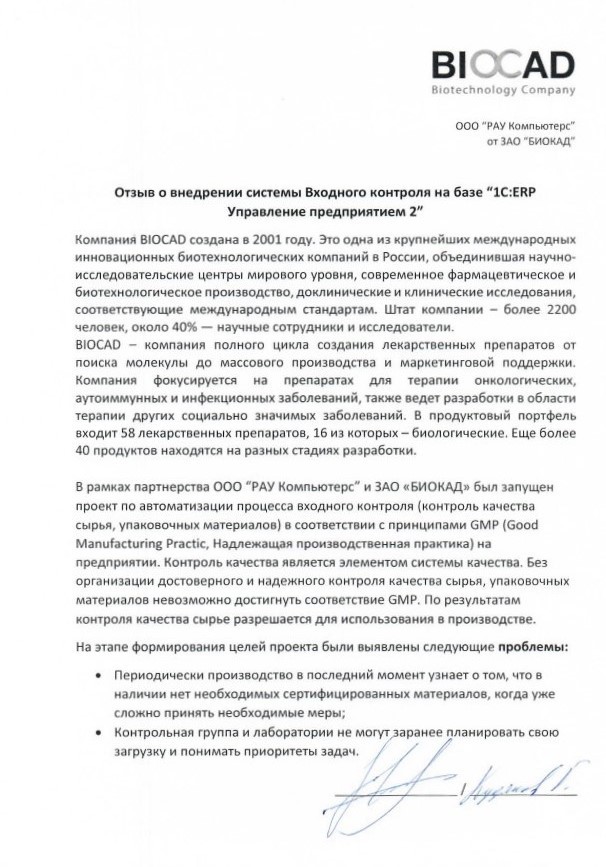
Подробнее о проекте на сайте 1С